Pardon the pun, but the hay baler and modern swather are intertwined with the High Plains Journal.
Today, hay equipment can be handled much easier because of greater mechanical and technology investment. At one time, many farm boys cringed when they thought about handling hay. The above photo shows several round bales near Dodge City, Kansas.
Bruce Anderson, a professor emeritus and Extension forage specialist at the University of Nebraska, grew up on a small dairy farm in southern Minnesota.
“My first recollection of hay was around age 6 or 7 in the late 1950s. Alfalfa was cut with a 7-foot sickle bar mower, maybe at 3 acres per hour,” Anderson said. “It then was raked with a single side delivery rake a couple days later and packaged into small square bales about one day after that. A hay rack was pulled behind the baler with one person gathering and stacking bales as they were made.”
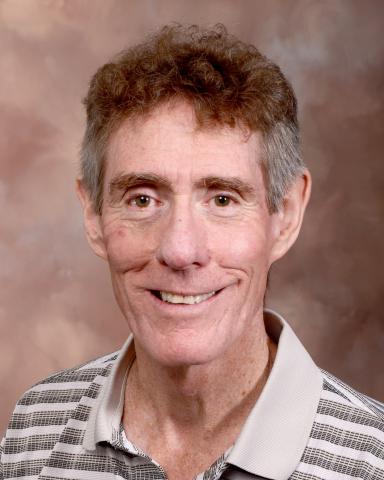
While this was his first recollection, the family had been using a baler for just a short time. Prior to that they would cut and bunch hay, gather it loose on racks and lifted it into the hay loft using slings.
“All that equipment was still on the farm and probably operational but never used during my youth,” Anderson said and quipped, “Thank goodness.”
Baler ownership was shared by his father and his two brothers who also farmed within seven miles of each other. They also shared ownership of a combine and corn picker, so all harvesting had to be coordinated amongst the three of them.
Round balers were not common in his area because most hay was devoted to dairy cows where small square bales facilitated better control for feeding and for storage under cover.
Round baler revolution
In 2018 in a story about the importance about the evolution—and some might say revolution—of farm machinery during the past 60 years, the introduction of round balers was near the top of Mount Rushmore of modern equipment.
The original patent was issued to Wesley Buchele, an agricultural engineering professor at Iowa State, who saw a major labor shortage occurring on the farm, said Carl Bern, a professor emeritus of agricultural and biosystems engineering at Iowa State University. Buchele, who grew up on a Kansas farm, also had a patent on the axial flow combine and was recognized by Iowa State as one of the most influential agricultural engineers in North America.
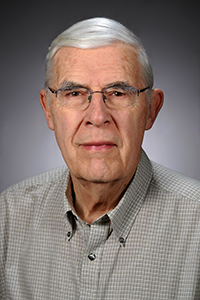
In the 1950s hay was assembled in 30- to 70-pound square bales that were tied together with wire or twine. The farmer, to be efficient, had to use young laborers to load the bales on a wagon and transport them to a barn, said Bern, who grew up on a farm in Wahoo, Nebraska.
“It was hard on your back,” Bern said. “I know, because I injured mine loading bale wagons.”
Buchele decided there must be a better way to put hay in a bigger package and take advantage of the mechanical advancements in tractors and attachments. Buchele and a graduate student went to work and their work produced a baler that allowed a farmer to feed the hay or corn stalks into the machine and make a much heavier bale.
The large round bales could be moved with an attachment to the tractor. Today’s modern balers can produce bales in excess of 2,000 pounds compared to the square vales that were less than 100 pounds.
“A single farmer could avoid the problem of not having enough labor to harvest the hay crop,” Bern said.
Windrowers advanced too
Dane Mosel, tactical marketing manager based in Gothenburg, Nebraska, with AGCO Corporation, said the late Lyle Yost, owner of Hesston Corporation, who purchased patents from an Iowa farmer for a self-propelled windrower in the early 1950s, was a pioneer. Hesston Corporation then launched the self-propelled windrower in 1955 kicking off a long history of hay equipment.
“Many industry firsts made their debut in the early years, one of the notables would be the double knot knotter system for the large square balers,” Mosel said. “The knotters developed in the early 1970s are almost identical to the knotters being installed on balers in Hesston today.”
Handling hay is different than other crops, Mosel said. To a certain extent hay equipment cannot get much larger because of the alfalfa to dry down in windrows. The future will likely feature multiple smaller units on one machine or to a leader-follower type setups to minimize labor inputs.
Sign up for HPJ Insights
Our weekly newsletter delivers the latest news straight to your inbox including breaking news, our exclusive columns and much more.
The baling side of production will continue to drive to more efficient large balers with increased capacity with increased capacity and multi-bale producing small square balers, he said.
Remarkable change
How the industry has changed has been remarkable. Mosel said one windrower in good alfalfa could cut 7 acres an hour in 1960. Today, a windrower can easily attain 25 to 30 an hour and certain triple mower setups can exceed 35 acres an hour, according to Mosel. For baling, farmers were excited to bale 6 tons an hour with a 15 by 16 small square baler. A modern round and large square baler can push 50 tons an hour of capacity.
Mosel said one aspect is that major manufacturers have not changed the design of small square balers, which means the majority of legacy balers should have a decent supply of parts. New Holland has built more than 750,000 small square balers in its history with many old machines still in use.
“The current (model) 1840 we offer isn’t too far off the original design from back in the early 1990s,” Mosel said.
Today’s needs
As livestock operations became larger and labor less available and more expensive, the biggest advances in hay making has been the size of the packages made and the speed (acres or tons per hour) at which material was handled, Anderson said.
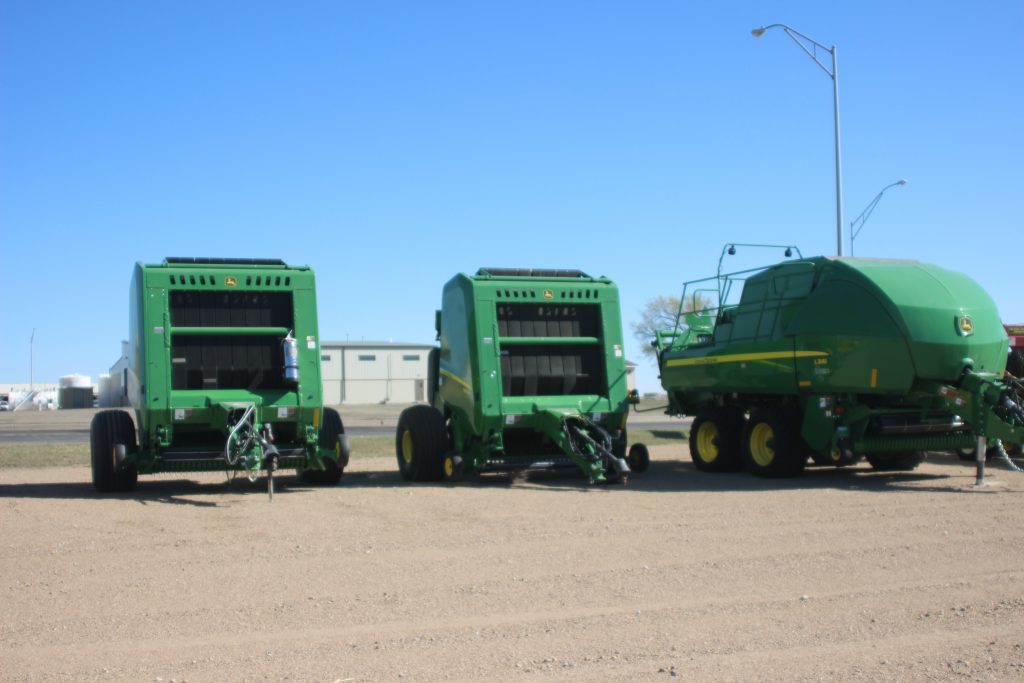
Big round and large square balers, windrow mergers, double or quadruple rakes, disc mowers sometimes connected five in tandem, steamers, bale carriers—are all designed for speed and volume, he said.
There still is room in the industry for small bales, Anderson said. Pleasure horses, alpacas, and llamas, thousands of small (less than 25 head) beef cow operations, hobby sheep and goat owners, and even wildlife and local zoos all might prefer small bales, especially if it is the right forage and right quality.
Anderson an advocate
One alfalfa hay harvest factor often overlooked is the needs of the end consumer or animal.
“As individual hay growers, we often get wedded to the desire for high quality, primarily because the dairy industry has strongly influenced our practices,” he said. “While there rarely is an overabundance of superior quality alfalfa hay, within an individual herd, even a dairy herd, there usually is room for various qualities of hay.”
With the growing emphasis on corn silage in dairy diets, fiber from alfalfa can become a more important component, lessening the need for supreme or premium quality hay, Anderson said. Beef producers can become misled into thinking they need higher quality hay than may be necessary, sacrificing yield for unneeded quality.
Dave Bergmeier can be reached at 620-227-1822 or [email protected].