On-farm innovation solves sorghum harvest struggles
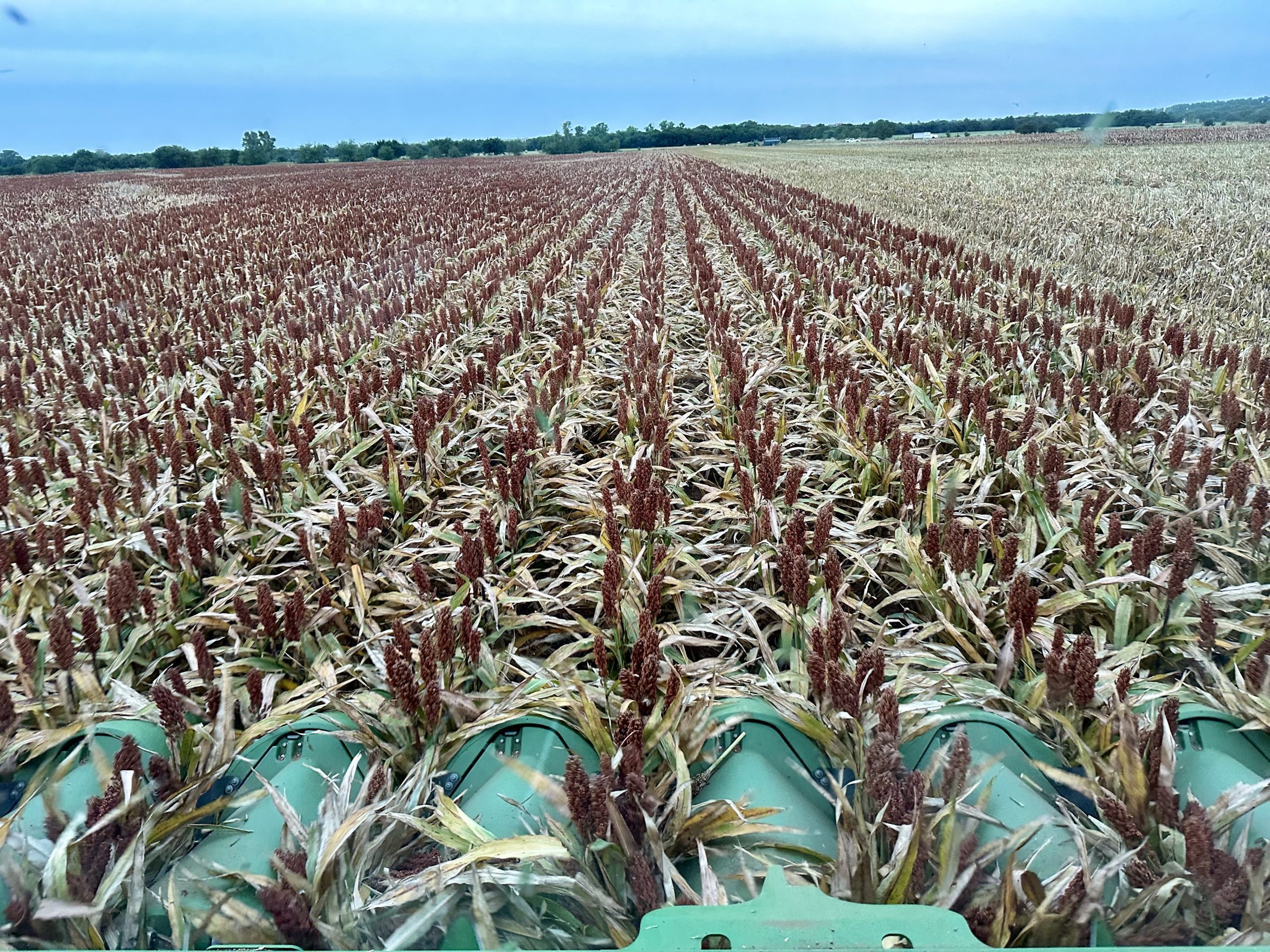
Every agricultural innovation—from the cotton gin to irrigation systems to gene editing—was devised to solve a problem and make production agriculture more efficient. Farmers and ranchers are the ultimate innovators when faced with challenges, and some of those creative solutions develop into products that benefit the inventor and other producers who grapple with the same agricultural difficulties.
Almost 10 years ago, three individuals designed the ARRO corn head conversion system—a product that continues to make sorghum harvest simpler for farmers across the world. It was 2015 when Kyle Kopper, of Cimarron, Kansas, became fed up with his row crop header. His father-in-law, Randy Burns, a long-time custom harvester and employee of Kopper Family Farms, and Alan VanNahmen, an agricultural engineer and product consultant, were both in the field when Kopper brought up his frustrations.
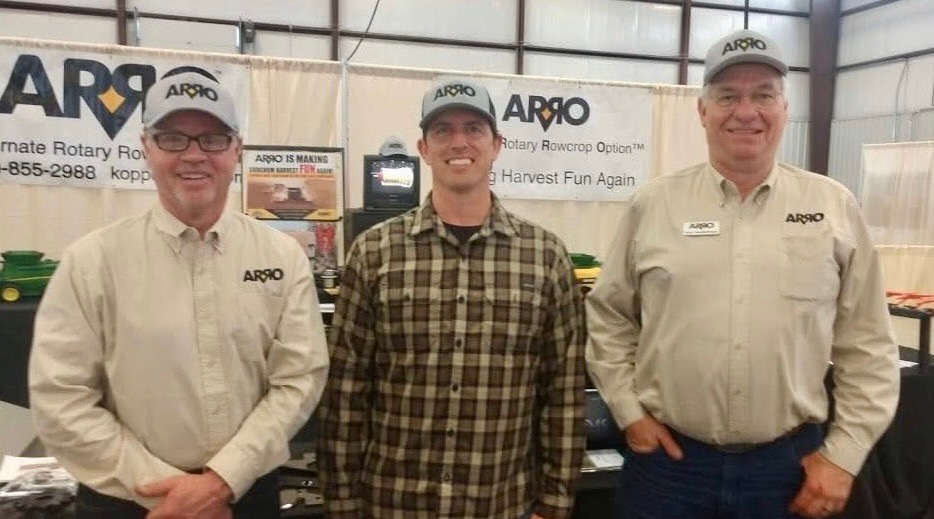
“It just seemed like one would break down, and we’d get it fixed, and we’d think we had it whipped, and then another header would break down,” Kopper said. “We always had the old row crop headers in the shop, doing preventive maintenance, replacing a bunch of bearings, and there was a lot of cost involved.”
Additionally, Kopper, like many farmers in the High Plains, uses no-till practices and is always looking for ways to leave more residue in his fields. Row crop headers cut extremely close to the ground and leave minimal residue. These headers were originally designed in the 1970s to harvest soybeans, but using them to harvest sorghum can be a challenge.
“John Deere row crop heads were designed to run 3 miles an hour, harvesting thin little soybean stocks for the most part,” VanNahmen said. “They have a hard time holding up when you start running 220-bushel sorghum.”
Kopper said when row crop headers first came out, they were designed for six or eight rows, but farmers started making them into 12- and 16-row headers, and this brought maintenance issues.
“Then if you put them on a 500-horsepower combine, something’s got to give, and sometimes it’s breaking the header down going through tough conditions,” Kopper said.
Getting ahead of harvest problems
The three men agreed there had to be a better way to harvest sorghum and resolve the issues the traditional row crop headers were creating. VanNahmen said major corporations like John Deere, Case IH, New Holland and Gleaner focus their attention on the No. 1 crop in the U.S., corn. He said in some ways, sorghum gets the shaft when it comes to equipment improvements.
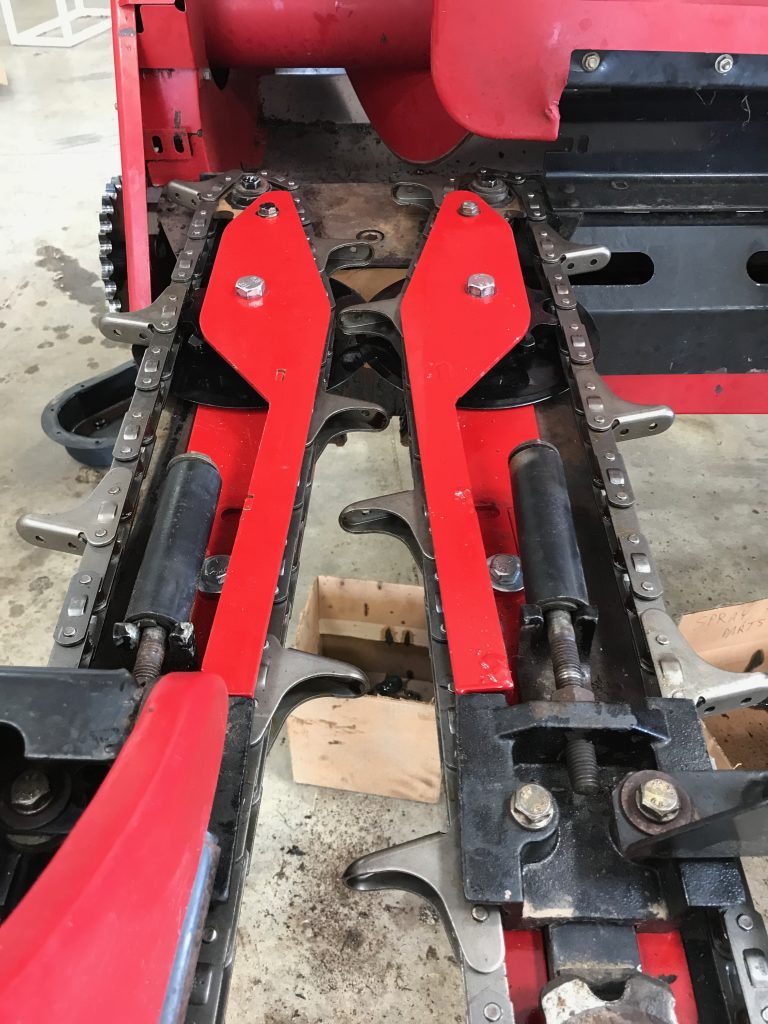
“Major manufacturers really didn’t want to spend much time going after sorghum, so Kyle, Randy and myself said, ‘We’ll take that on,’” VanNahmen said. “We wanted to make sorghum harvest fun again.”
Although the trio had originally discussed modifying a row crop header, it became apparent the better option would be to adapt a corn header to harvest sorghum.
“Corn headers are just so reliable,” Burns said. “I used to cut about 4,000 acres of corn every year, and you just didn’t have much trouble with corn headers. So that’s when we started playing with this, and things took off.”
After some brainstorming, modification and experimenting with a corn header, they settled on a dual-disk cutter design that could convert a corn header into the ultimate sorghum header.
Each of the twin 9-inch diameter cutting discs per row have over 28 linear inches of synchronized cutting surface per blade, turning together like self-sharpening, endless scissors to cut the toughest stalks and help feed the heads smoothly into the combine auger using the original gathering chains.
“We wanted to leave additional residue in the field, so we moved that cutting mechanism back towards the rear of the row unit, so that way we can leave at least 12 to 15 inches of stalk standing,” Kopper said.
The design works particularly well in heavily lodged or down sorghum, which is challenging to harvest with a row crop header. After finding a design that solved their problems and left additional residue, they modified a few corn headers, and other farmers started using them. Eventually, it became clear this was an innovation that was marketable and needed in sorghum production.
“You never know what other people are struggling with out there,” Kopper said. “If you have something that’s working for your farm, chances are, there are going to be other farmers out there that are looking for the same solutions.”
Kopper Kutter
From there, Kopper Kutter, LLC was born, and Kopper, Burns and VanNahmen became partners in the business. Kopper serves as the CEO/chief financial officer, Burns is the service manager, and VanNahmen is the marketing manager.
Burns said the ARRO name is two-fold. It stands for alternate rotary row crop option, but he is also a fan of the Kansas City Chiefs and liked the idea of naming the product partially after Arrowhead Stadium.
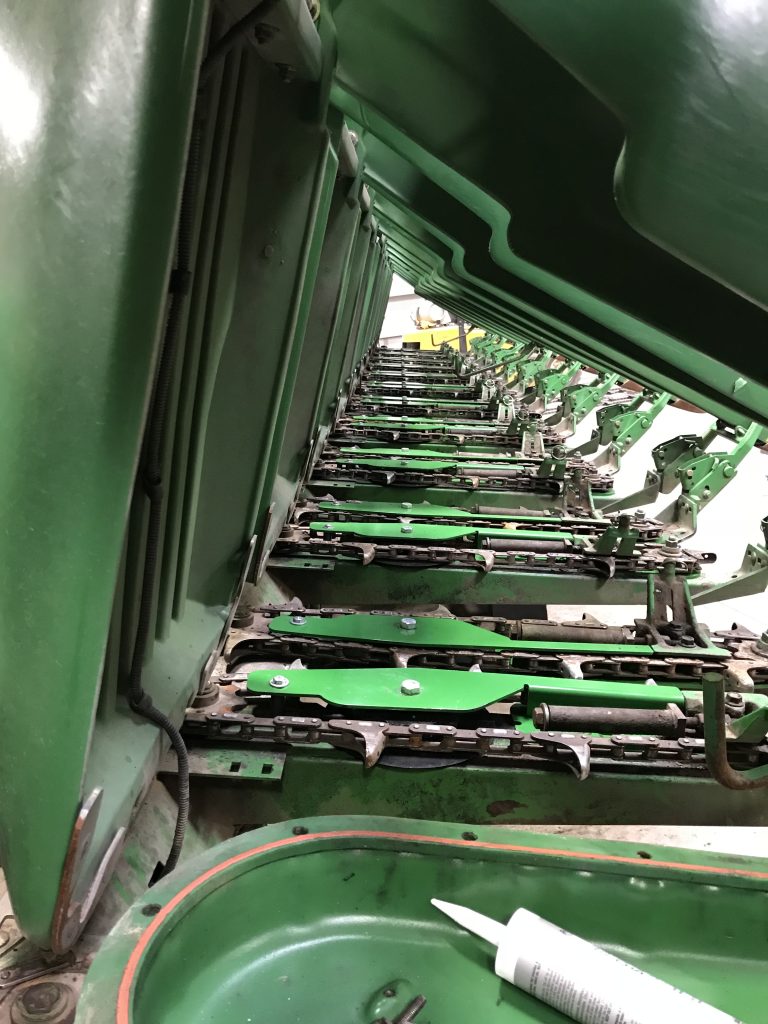
Kopper Kutter started manufacturing and selling conversion kits in 2017. VanNahmen has years of experience in agricultural product development, and, through his expertise, Kopper Kutter has received three patents on the ARRO system. Producers can use the conversion kit to harvest sorghum and sunflowers.
The ARRO conversion kit is compatible with most late model corn headers including: John Deere 40 and 90-series, Deere 600C series, including all 608C, 612C, 616C and 618C; Case IH 1000, 22 and 24-series, 32- and 34-series, 44-series; New Holland 96C, 98C and 99C; CLAAS corn heads for Lexion and CLAAS combines, Models 8-30, 12-30 and 16-30; AGCO Gleaner Hugger and Drago corn heads.
Producers can purchase the ARRO conversion kit and install it themselves, purchase a corn header and hire Kopper Kutter to do the installation or purchase a modified corn header from a dealership.
To convert a corn header, the original stalk rolls and factory deck plates are removed from the header. The factory chain guides and gathering chains are detached and set aside. Next, the stalk roll drives are removed from the row unit gear cases and replaced with the cover plates provided in the kit.
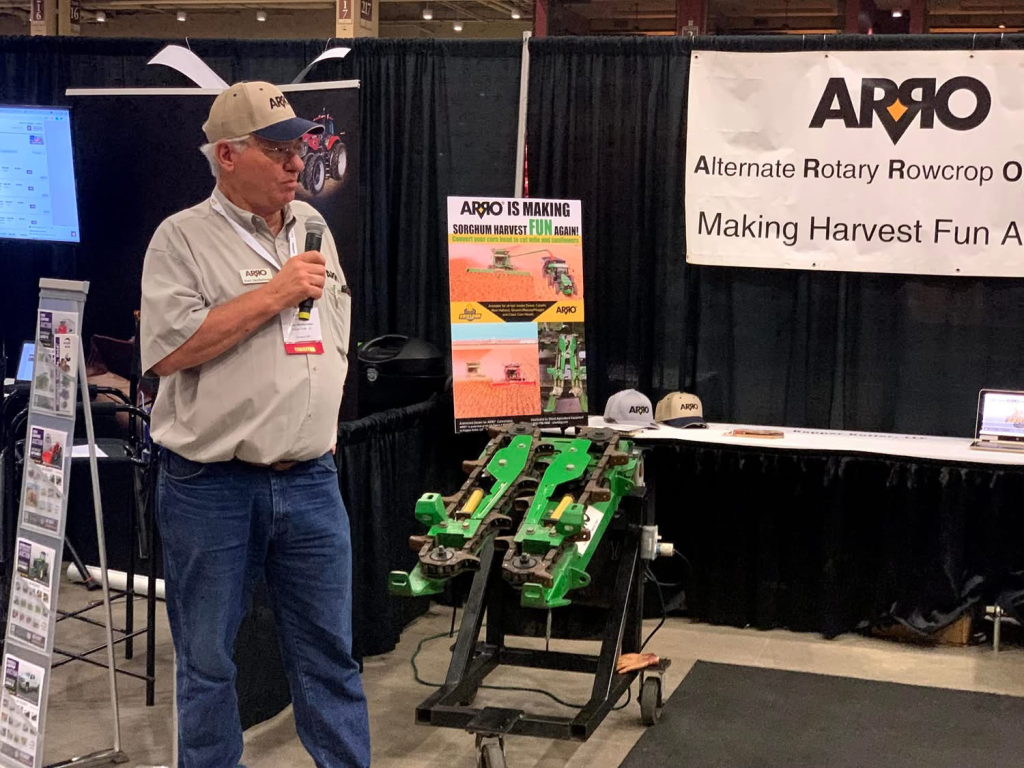
Finally, new holes are drilled so the ARRO deck plates, disc and sprocket assemblies, chain guides, OEM gathering chains and chain tensioner assemblies can be installed. The conversion can be accomplished in two to three-man hours per row.
“We have a lot of farmers that have installed the kits themselves,” Kopper said. “It’s a fairly simple conversion, and once you get one row done, it’s like rinse and repeat.”
Used OEM corn headers ready for a rebuild are ideal candidates for the ARRO conversion kit. Additionally, conversions cost one-third to half the price of a new row crop header, and the simplified mechanics of the converted header often lead to less maintenance on combines.
“A guy who normally ran a straight header borrowed a converted header from me, and he told me he figured he was sending 50% less material through the combine,” Burns said.
Less material running through the combine means less wear and tear on the equipment, fewer breakdowns, faster running speeds and fewer separator hours—increasing harvest efficiency.
Bringing ideas to market
The ARRO is just one innovation success story that demonstrates the creative problem-solving abilities farmers and ranchers apply in their daily work.
“If it’s working for you, it’s probably going to work for other people,” Burns said. “That’s how we all get better in this world. We build off each other’s ideas.”
VanNahmen, who grew up in Spearville, Kansas, has 45 years of agricultural engineering experience and has been helping farmers and ranchers bring their agricultural product ideas to fruition for decades. In 1991, VanNahmen started a consulting company called Farm Buddy. Through the business, he advises agriculturists who need assistance with new product development, patents and guidance.
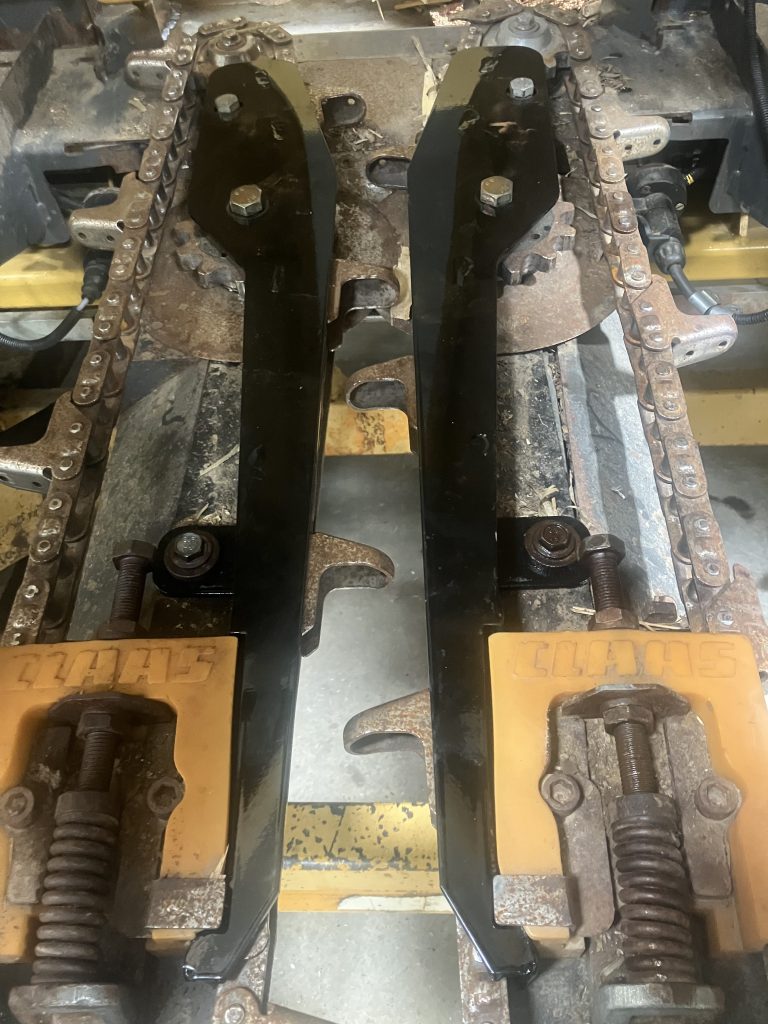
After years of working for equipment companies like John Deere and CLAAS, VanNahmen saw a need to help individuals with their ideas and mentor them through the process.
“There are a lot of farmers that were bringing product ideas to their dealers or the equipment company, and they didn’t really didn’t have a way to protect their intellectual property,” VanNahmen said.
While he was working for John Deere, he was often sent to farms to resolve issues farmers were having with their equipment. Sometimes the farmers would recommend solutions or changes to the design of the equipment, and VanNahmen would report those recommendations to his supervisors.
“Then lo and behold, three or four years later the equipment would be updated with their ideas, and those farmers would say, ‘I showed you how to do that or what to do,’ and I said, ‘You know, you’re absolutely right, but you didn’t have any non-disclosure agreement or confidential agreement in place, and it’s just the way the world works.’”
VanNahmen said he has helped around 50 farmers with their product ideas and inventions over the years. His advice to anyone with a clever farm idea or invention is to talk to other industry professionals early on in the process and document the details of their innovation with proof of its origin.
“They need to make a sketch and date it, and probably have that signed by either a family member or co-worker, so they can protect that idea and show that they had it,” VanNahmen said. “A model or prototype of it is good, too. Then, contact a patent attorney.”
VanNahmen recommends inventors require others to sign a confidentiality agreement or non-disclosure agreement to protect sensitive information about a product or idea, especially early in the process.
To learn more about the Kopper Kutter and the ARRO conversion kit, visit www.kopperkutter.com or contact Randy Burns at 620-255-2435.
Lacey Vilhauer can be reached at 620-227-1871 or lvilhauer@hpj.com.